جایگاه صنعت کاشی و سرامیک در ایران:
صنعت کاشی و سرامیک بهعنوان یکی از صنایع پیشرو در ایران شناخته میشود. کارشناسان انتظار دارند که با افزایش تولید کاشی و سرامیک و همچنین بهبود روند صادرات آن در کشور که در حال حاضر ایران بهعنوان یکی از پنج کشور برتر تولیدکننده در زمینه کاشی و سرامیک شناخته میشود، بتوان ارزآوری این صنعت را افزایش داد. صنعت کاشی و سرامیک به دلیل وجود منابع معدنی ارزان و فراوان، دستمزد پایین نیروی کار، منابع انرژی ارزان و حاشیه سود مناسب ، پتانسیل مناسبی را برای رشد و توسعه در بازارهای جهانی را دارا میباشد. طبق آخرین آمار اعلامشده از سوی انجمن صنفی تولیدکنندگان کاشی و سرامیک کشور، ایران با تولید ۳۹۸ میلیون مترمربع کاشی و سرامیک در سال ۲۰۱۹، ۳.۱ درصد از تولید این محصول را در جهان به خود اختصاص داده است و با این میزان از تولید، رتبه هفتم جهان پس از چین، هند، برزیل، ویتنام، اسپانیا و ایتالیا را در اختیار دارد. با توجه به وجود پتانسیل زیاد رشد در صنعت کاشی و سرامیک و جایگاه مهم آن در کشور، بررسی روند تولید محصولات مرتبط با این صنعت میتواند برای تولیدکنندگان و علاقمندان به این حوزه از اهمیت ویژهای برخوردار باشد.
مواد اولیه اساسی در تولید کاشی و سرامیک:
ماده اولیه اصلی جهت تولید کاشی و سرامیک از انواع گوناگون خاک بدست می آید که در شرایط خاص و ویژه ای از معادن استخراج میشوند. کاشی و سرامیکها بر اساس کاربرد و نقشی که دارند، از مواد اولیه متفاوتی ساخته میشوند که عبارتند از: مواد اولیه پلاستیک، پرکننده یا فیلرها و کمکذوبها یا گدازآورها که در ادامه به شرح آنها پرداخته خواهد شد ولی در ابتدا بهتراست جنس خاک مورداستفاده در تولید این محصولات و علت استفاده از آن بررسی شود .
یکی از بهترین خاکهای مورداستفاده در این صنعت خاک رس میباشد. رس نیز مشابه سایر خاکهای دیگر از فرسایش و هوازدگی سنگها مخصوصاً سنگهای آذرین طی سالیان دراز به وجود آمده است. از دلایل عمده استفاده از خاک رس در این صنعت، وجود بنیانهای مولکولی Sio2,Al203 در ساختمان رسها می باشد که بعد از پخت، فازهای بسیار سخت سیلیکاتی را تولید نموده و موجب افزایش مقاومت در محصولات میگردند.
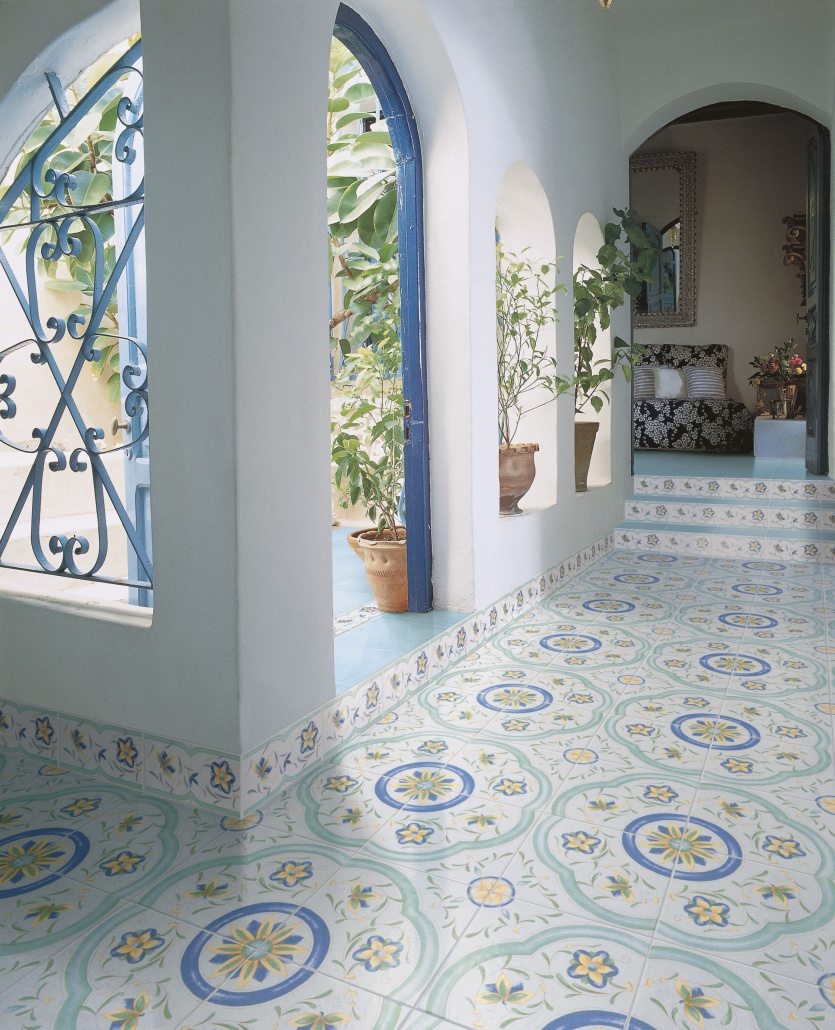
کانیهای رسی با سختی تقریباً یک موجب ورود این بنیانها در فرمول بدنه میگردند. درحالیکه اگر بخواهیم همین مواد را بهطور خالص که بنام کوارتز و کراندم با سختی به ترتیب 7 و 9 میباشند در فرمول وارد کنیم سایش آنها تقریباً غیرممکن و بسیار هزینهبر خواهد بود. بنابراین هزینه خریداری رسها بسیار بهصرفهتر از مواد دیگر است. در بین کانیهای موجود در طبیعت، رسها بسیار ریزدانهترند و در برخی موارد میلیونها برابر کوچکتر از سایر کانی ها می باشند و از طرفی بهواسطه شکل لایهای موجب ایجاد یک دوغاب هموژن میگردند که زمان تهنشینی آن بسیار طولانی است درحالیکه مواد دیگر چنین خاصیتی را ندارند.
مواد پلاستیک: منظور از پلاستیک همیشه به معنی مواد پلاستیکی مشتق از مواد نفتی نمیباشد. درواقع پلاستیک همان خاصیت پلاستیسیته خاک رس است. پلاستیسیته خاصیتی است که به یک ماده قابلیت میدهد تا در اثر یک نیروی بیرونی بدون شکست و تخریب، تغیر شکل داده و بعد از حذف یا کاهش آن نیرو همچنان حالت خود را حفظ نماید.
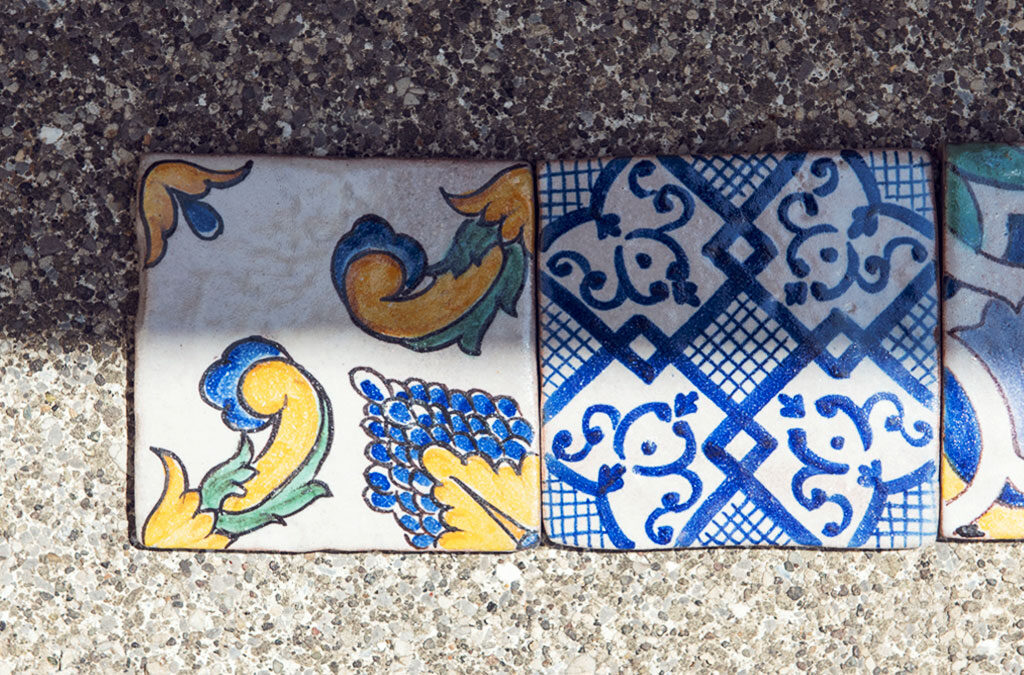
پرکنندهها یا فیلرها: این مواد برعکس گروه اول، غیر پلاستیک بوده و نقطه ذوب بالایی دارند. پرکنندهها همچنین در مقابل مواد شیمیایی و محیطهای اسیدی مقاومت بالایی را از خود نشان میدهند. مهمترین وظیفه پرکنندهها در مرحله اول جلوگیری از تغییر شکل بدنه در طول پخت، انبساط حرارتی مناسب و کنترل انقباض تر به خشک و خشک به پخت میباشد و در مرحله دوم پرکنندهها در تعیین تخلخل و رنگ (سفیدی) بدنه اتصال مناسب لعاب و بدنه و اصلاح بافت بدنه خام و… نیز نقش بسیار مهمی را ایفا مینمایند. مهمترین پرکننده در این صنعت سلیس و آلومین (کروندوم) میباشد، چراکه در حین پخت به سرامیک کمک میکنند که کمترین تغییر شکل را داشته باشد و همچنین باعث بالا رفتن چسبندگی بین بدنه سرامیک و لعاب میشوند.
گدازآورها: موادی هستند که به جهت کاهش نقطه ذوب بدنه و یا لعاب، مصرف بالایی در این صنعت دارند. گدازآورها در هنگام پخت بدنه ذوب گردیده و در هنگام سرد شدن فاز شیشهای را در بدنه به وجود میآوردند که کلیه بلورهای موجود در بدنه پختهشده را در برگرفته و بدین ترتیب موجب افزایش استحکام محصول نهایی میگردند. نقش اصلی این مواد درواقع کاهش نقطه ذوب میباشد. از عمده گدازآورها میتوان به :
• اکسیدهای پتاسیم
• سدیم
• کلسیم
• منیزیم
اشاره کرد که جهت تأمین آنها از فلدسپاتهای سدیک، پتاسیک و کلسیک استفاده میشود. اما غیرازاین مواد، موادی نظیر کربناتها مثل کلیست و دولومیت نیز در بدنه کاشیهای دیواری مصرف میشود که نقش تأمین جذب آب را در این کاشیها ایفا مینماید.
دستگاههای مورداستفاده در کارخانههای کاشی و سرامیک:
در کارخانههای کاشی و سرامیک برای تولید محصولات خود از ماشینآلات پیشرفته مخصوص هر مرحله استفاده میشود؛ این دستگاهها به ترتیب استفاده در مراحل ساخت سرامیک عبارت از: “سنگشکن، باکسفیدر، بالمیلدوغاب و لعاب، اسپری درایر، دستگاه پرس، کورههای رولری و تونلی، خط لعاب و دکور زنی، دستگاههای مربوط به بستهبندی و درجهبندی” می باشند.
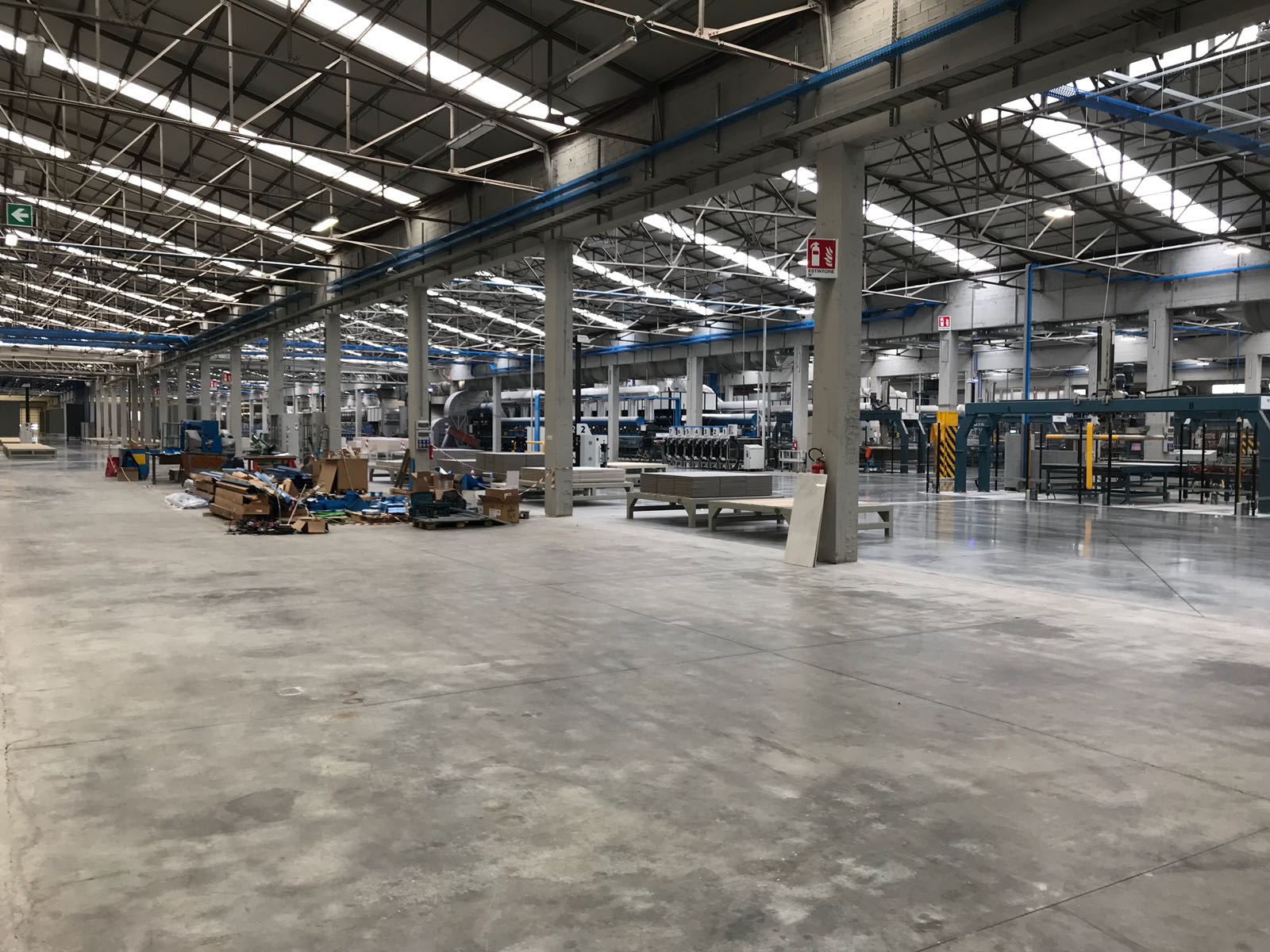
مراحل تولید کاشی و سرامیک:
آمادهسازی پودر: منظور از آمادهسازی مواد اولیه اعمالی است که بعد از ورود مواد اولیه به کارخانه و قبل از توزین و اختلاط آنها، انجام میگیرد این مرحله اولین مرحله در خط تولید کارخانههای تولید کاشی و سرامیک بوده و بهطور عمده شامل خرد و آسیاب کردن مواد است. در مرحله آسیاب مواد که بیشتر در مورد مواد سخت و دانهدرشت بکار میرود توسط مقداری از سنگشکنها مواد درشت به مواد ریز تبدیل میگردند. سنگشکنهای مختلف رایج در صنعت سرامیک، فکی، چکشی، مخروطی و غلتکی و دوار و…میباشند. در آسیابها مواد خرد شده به همراه آب و مقدار مشخصی از روانسازهایی چون سیلیکات ، تری پلی فسفات سدیم Tpp، کربنات سدیم با دور و سرعت مشخص تحت سایش قرار می گیرند و به دوغ آب تبدیل می شوند. مقادیر این مواد دقیقاً از قبل تست و مشخص می گردند. کیفیت مواد ورودی، درصدهای اختلاط، مشخصههای محصول سنگشکن و خصوصاً مشخصههای دوغاب پس از آسیاب نظیر دانسیته، ویسکوزیته و دانهبندی نیز دقیقاً کنترل میشود. در ادامه جهت آمادهسازی پودر از دوغاب از خشککنهای افشان یا پاشنده یا اسپری درایر استفاده میشود. دوغاب حاصل از آسیابها پس از دپو در مخازن دوغاب وارد مخازن دوغاب اسپری درایر میگردد. پمپهای پیستونی با فشار نسبتاً بالا دوغاب را به محفظه استوانهای اسپری درایر اسپری نموده و دوغاب پس از برخورد با هوای داغ و تبخیر آب به پودر با رطوبت مشخص و دانهبندی مشخص تبدیل میشود.
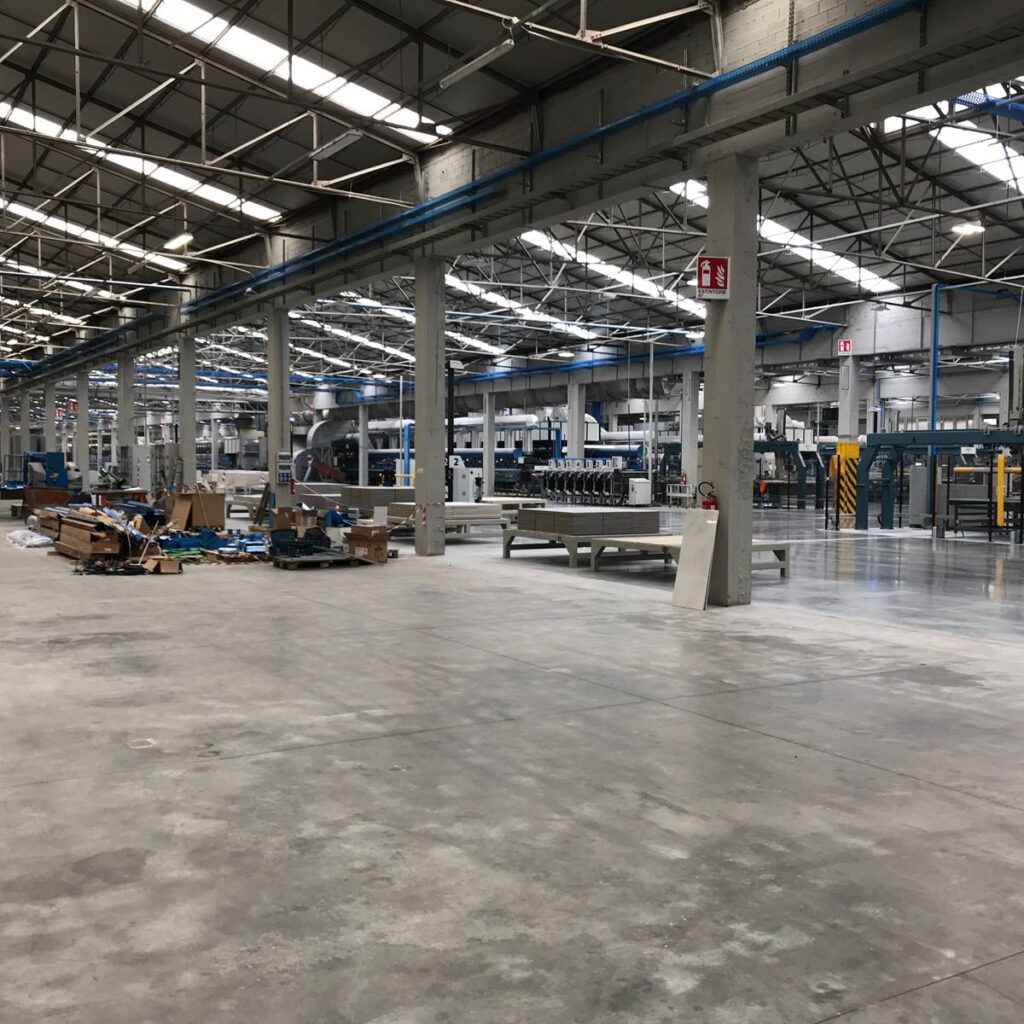
پرس و شکلدهی قالب اولیه کاشی و سرامیک: در این روش مخلوط مواد اولیه که بهصورت پودری با دانهبندی مناسب درآمده در حفرههای قالب و تحتفشار قرار گرفته و بدین ترتیب شکل قالب را به خود میگیرند. امروزه در صنایع تولید کاشی، پرسهای بسیار مدرن و با توانمندیهای بالا وجود دارد که حتی میتوانند طرح را در مرحله پرس کردن بر روی کاشی ایجاد نمایند.
خشککردن کاشی سرامیک: اگر قطعه کاشی بهخوبی خشک نشود یا با سرعت بالا خشک شود موجب ایجاد ترک شده و یا میپیچد یا تغییر حجم میدهد. اگر قطعه را پس از خروج از پرسکاری با حرارت خشک کنند یا در معرض هوای خشک و گرم قرار دهند سطح خارجی آن بهسرعت خشک می شود لذا برای خشککردن قطعات مرغوب از تونل هوای گرم استفاده می کنند. برای جلوگیری از ترک برداشتن و چروک شدن و پیچش سطحی، هوای ابتدای تونل کاملاً مانند هوای خارج است. در وسط تونل، حرارت به حداکثر لازم میرسد و در این مرحله کلیه آب موجود در قطعه متصاعد شده و کاملاً خشک میگردد. در مسیر تونل رطوبت و حرارت موجود باید اندازهگیری میشود.
لعابکاری و اصلاحات هندسی: در کاشیهای تک پخت مانند نمونه کاشی دیواری منوپروزا (تک پخت)، کاشیهای کف و پرسلان لعاب دار پس از مراحل خشک کاری، کاشی، وارد مسیر آبی میشود و سپس لعابکاری آستری که به آن آنگوب نیز میگویند روی آنها انجام شده و به دنبال آن لعابکاری اصلی توسط دستگاههای دیگر با استفاده از طرحهای موردنظر، به وسیله دستگاه های مخصوص روی کاشی و سرامیک انجام میشود. ماشینآلات جدید که برای لعابکاری مورداستفاده قرار میگیرند دارای قابلیت چاپهای بیشتری روی کاشی می باشند.
پخت سرامیک و کاشی مورداستفاده: بعدازاین که لعابکاری انجام شد، نوبت به پخت کاشی و سرامیک میرسد. اساس پخت کاشی منحنی زمان-دما است که به آن منحنی پخت کاشی نیز میگویند و این منحنی برای محصولات مختلف و کاشیهایی با استفادههای مختلف متفاوت است و با توجه به دماها و تنظیمات لازم موجود در دیوارهها یا سقف کوره در نظر گرفته میشود. بازده و راندمان پخت کاشی به انرژی گرمایی بستگی دارد که توسط محصولاتی که در کوره قرارگرفتهاند جذب میشود.
درصورتیکه در این مرحله توجه کافی به موضوع پخت نشود و اصول لازم برای انجام این کار رعایت نشود ممکن است که به مشکلاتی مانند: استحکام کم و ترد و شکننده بودن، شفافیت و موارد مربوط به درخشندگی سطح، تغییر طیف چاپ و زمینه، گونیا نبودن و اختلاف سایز، کثیف بودن سطح لعاب، وجود نقاط سیاهروی لعاب، ترکهای مویی لعاب ترکهای مکانیکی و شکستگی و گوشه پریدگی، دفرمگی و تابدار شدن کاشیها برخورد کرد.
پولیشکاری: زمانی که پولیشکاری انجام میشود روزنههایی که احتمالاً روی سطح وجود دارد موجب کاهش عمر کاشی و سرامیک و نفوذ آب در آن می باشند، بسته میشوند و سرامیک یکدست میشود.
سورتینگ Sorting : سورتینگ اصطلاحی است به معنای درجهبندی و دستهبندی محصولات بر اساس اندازه، رنگ، شکل ظاهری و سایر عوامل و جداسازی. در صنعت کاشی و سرامیک پس از تولید محصول ، هر کاشی بر اساس کیفیت تولیدشده طبق استاندارد درجهبندی میشود و توسط دستگاههای مدرن و استاندارد سورت میشوند. کاشیهای بدون مشکل در سورتینگ درجهیک قرار میگیرند و به کاشیهای کیفیت پایینتر درجههای دو، سه و چهار اطلاق میگردد.
بستهبندی: محصول تولیدشده پس از سورت شدن و دستهبندی درجه ، بستهبندی میشود، هر محصول نسبت به سایز و وزن آن در کارتن قرارداده شده و بستهبندی میشوند.
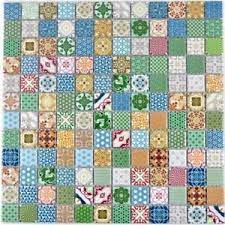
سخن آخر
نحوه ساخت و تولید کاشی سرامیک از زمانهای قدیم تا به امروز علیرغم پیشرفتهای زیاد در ماشینآلات و ابزارهای موردنیاز این صنعت همچنان یکی از دغدغههای اصلی این حوزه محسوب میشود. از سوی دیگر این صنعت در زمره صنایعی است که بیشترین نقش را در شاخصهای منتخب ازجمله سهم ارزشافزوده، اشتغالزایی، صادرات، سهم از بازار، مزیت نسبی و زنجیره تأمین (بهعنوان مواد اولیه یا کالاهای نهایی) و سطح دانش و فناوری داراست. بر همین اساس سرمایهگذاری و ورود به این صنعت و همچنین گسترش اطلاعات در خصوص نحوه تولید کاشی و سرامیک سبب افزایش رشد اقتصادی کشور در سالهای پیش رو خواهد شد.
افکارتان را باما در میان بگذارید
برای افزودن دیدگاه باید وارد شوید .